Onsite Steelfab has invested in the future by investing in its first state-of-the-art CNC equipment. Through the use of an ART high definition CNC plasma cutter, Onsite has increased its productivity, reduced cycle times and improved accuracy, which will assure the small steel fabrication shop’s success in the long term.
In order to survive in today’s competitive marketplace, small steel fabrication shops must find ways to increase productivity without sacrificing quality. “People aren’t going to accept long delivery times or second best anymore,” says Mick Robinson, owner of Onsite Steelfab in Bayswater, VIC. “You have to exceed the customer’s expectations, especially in turnaround times, or they’re going to go somewhere else.”

ART’s former Victorian Sales Manager, Guy Garreffa (left) and Onsite Steelfab Manager and owner Mick Robinson in front of the company’s first CNC machine: an ART 8500 HDP heay-duty plasma cutter, which has transformed Mr Robinson’s business.
Founded in the early nineties by Mr Robinson, Onsite Steelfab today services the telecommunications industry with steel structures and parts for radio transmission towers and poles in Australia. Onsite’s customer base is the contractor market for Telstra, Optus and Vodafone, among others. At present, Mr Robinson employs five people, including two apprentices and a new operator for his recently installed ART CNC plasma cutter. “We are very much a traditional, family-owned, small fabrication shop,” Mr Robinson says. He recently sold the other arm of his business, Tipper Tarps Load Cover Systems, as he wanted to concentrate on the steel fabrication side of the business.00
Faced with a shop with aging manual machines that finally started to cause financial, safety-related and operational troubles, Mr Robinson knew it was time to invest in up-to-date CNC equipment. “We used to produce our parts by keeping around 15 different flatbar sizes in stock, which were then fed through the hydraulic shear for cutting,” Mr Robinson explains. “Obviously, this didn’t only limit the variety of parts and shapes we were able to produce, but also faced us with safety issues, high levels of stock and longer turnaround times.”
After manually cutting00 the flatbar steel sheets, Mr Robinson was left with sharp workpiece edges, which had to be manually deburred, adding additional time to the fabrication process. Moreover, accuracy was another issue, especially with hole positions, while certain features such as slots were impossible to mach0ine with the existing equipment.
“There aren’t many options for companies our size. check this site for more information related to the technology related artical .If you’re going to stay busy, and continue to meet the customer’s needs, you have to invest in new technology and equipmen00t. It’s like continuing your education,” Mr Robinson says. “For small companies, the future depends on modernisation.”
“We compared different locally-made CNC plasma cutters,” he says. “We felt that by buying locally, we would have the prompt service we need to keep our machine running. We knew the reliability of ART plasma cutters and routers from talking to people in our industry.”
The decision between two local CNC plasma cutter manufacturers eventually went in favour of the ART 8500 HDP heavy-duty plasma cutter; not based on price, Mr Robinson emphasises. “The ART machine came with a higher price tag than the competitor’s, but as it is with everything in life: you get what you pay for. The robust structure and additional features like the fume extraction system and an easy-to use controller convinced me to spend the extra dollars.”
“Moreover,” he adds, “the ART team offers excellent service and training, and I felt very comfortable in dealing with them.”
ART has developed the high definition CNC plasma cutter range specifically for heavy-duty manufacturing environments such as found at Onsite, where power, precision, speed, quality, low cost, productivity and durability are demanded by business owners.
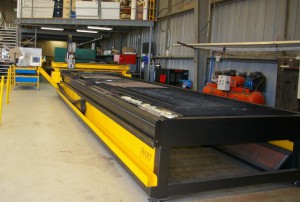
ART has developed the high definition CNC plasma cutter range specifically for heavy-duty manufacturing environments such as found at Onsite, where power, speed, quality, low cost, productivity and durability are demanded by business owners.
The HDP plasma cutter offers precise heavy-duty cutting of steel, stainless steel and aluminium and comes with a process area from 3700mm x 1900mm up to 15000mm x 3200mm. The machine delivers economic processing of high-standard cut components with an edge quality that is comparable with laser cutting. Moreover, an efficient fume extraction system ensures the air is kept clean at all times.
Mr Robinson is very impressed with the performance and would never go back to manual cutting.
“I’m over the moon,” he says. “The machine has transformed the way we work! It has helped us cut out many operations and reduce our stock level. That saves a lot of money and time. It’s made a huge difference in our company. It replaces at least one or two workers on the floor.”
Most importantly though for someone like Mr Robinson, who has worked hard all his life but never operated CNC machines or CAD/CAM software, ART’s machines are easy to operate and the software and controller are intuitive. ART machines feature both touch screen and pendant control, providing a quick and simple means of entering machine instructions, editing parts, moving, resizing and more, all at the machine or remotely from the PC.
“ART ProfileShop CNC controller software is an amazing user interface that is so simple to use,” Mr Robinson says. “After one week of training, I was able to draw and cut simple shapes, and whenever I had a problem, ART was there and helped me online or over the phone. They offer fantastic support and service.”
Onsite Steelfab now predominantly serves interstate markets in Perth, Sydney and Brisbane, simply for one reason, Mr Robinson concludes. “We have a reputation in the market and turn our steel around quicker than our competitors interstate. Since we installed the ART CNC plasma cutter we can process the steel twice as quick – and it even allow us to source additional contract work. It really transformed our business.”
More information on ART CNC plasma cutters here
Download Onsite Steelfab case study
Share