One of the most common forms of automation that has found its way into many manufacturing facilities is the CNC router. These machines have revolutionised cutting and drilling processes for materials such as aluminium, timber, plastic and composite panels, thereby reducing manual labour and improving accuracy and efficiency. Unfortunately, fast processing times are often hampered by delays in material handling such as loading and unloading material. Investing in automated sheet loading systems can enhance the flow of material across the router table and bring greater a greater return on investment.
By David White, Director of Advanced Robotic Technology (ART), Brisbane
AUTOMATION is a word that immediately comes to mind when we think about improving productivity and profitability in the manufacturing sector. When considering whether the purchase of a piece of automation equipment such as a CNC router makes sense, price alone does not tell the whole story. Profile cutter automation earns returns in various ways, some of which will be more or less valuable to different businesses, and all of the returns on automation deserve to be figured into the analysis.
There are a lot of different things that a wooden pallets manufacturer will be doing for several industries. Every company needs to have a way to ship their finished product. They also need to have a way to receive their raw materials, like those they get from companies like https://www.cir.net/fresno-branch/.
Pallets come in many different shapes and sizes. They also come from many parts of the world. The type of wood that is used to make them will vary greatly too. Click here if you want to get more about pallet manufacturing company Unaka Forest Products.
Many of them are made with wood that cannot be sold for construction or other products. It may have spots that are damaged but they can still support products. There are a lot of places that will order pallets. Others may reuse the ones that their raw materials come on.
Some larger companies will rent pallets from companies to use. If they need to have a certain quality of pallet, they will need to find a company that can supply them what they need. There are many different grades of pallets.
The finished products will be stacked onto a skid. The size of the product will determine how many of their products will fit on each pallet. Some products are large enough that only one will fit on there.
Of course, the absolute pinnacle of automation is the chance to keep producing while the machine is unattended. But even if this is not the immediate goal, there can be wide ranging benefits for investing in cnc machining, as well as an automated sheet loading system. Although this might make the CNC router seem more expensive, it can quickly bring returns on investment through improved productivity in a number of areas
The various sources of return on investment for automated material handling include the following:
Speed. Especially when handling heavy sheets, manual loading might not be an option because the machine sets the pace and operators may struggle to keep up with the machine. More significantly, the automatic loader does not get tired. Its speed remains the same, even late into the shift.
OH&S. Many materials are too heavy to be manually loaded safely by a single operator. This means tying up multiple employees or risking work related injuries and that’s why the use of legal resources from this Source could be really helpful with this. Automated material handling means no heavy lifting and no back injuries.
Consistency. How valuable is it to be able to accurately predict how long the entire production run of a part will take? Knowing just the machining cycle time is not enough to make this prediction. The amount of time between each cycle – that is, the load and unload time – is a variable as long as it relies on human beings. This variable is influenced by which operator is doing the loading, how the operator is feeling at that moment and to what extent the operator gets distracted. By contrast, automation turns the load/unload time into a fixed and repeatable value (in addition to potentially shortening this time). You can use volume hiring Salt Lake City services in order to gain access to the recruiter’s insider knowledge of skilled available candidates both active and passive, salary ranges, and local market trends.
Increased output per operator. A plant that depends on operators to load its machines has to add both machines and people in order to increase its volume. Moreover, for large, heavy part applications two or more operators may be required in order to load and unload the part to and from the machine. However, a business that uses at least some automation can add machines without necessarily adding people, making it that much easier to quickly respond to increasing demand.
In general and in particular for parts with short cycle times, the principle reason to automate is productivity. If the sheet is relatively lightweight, an automated system is likely to load and unload the blanks and sheets faster than a human being can, and this loading time advantage will accumulate over time.
The ART solution
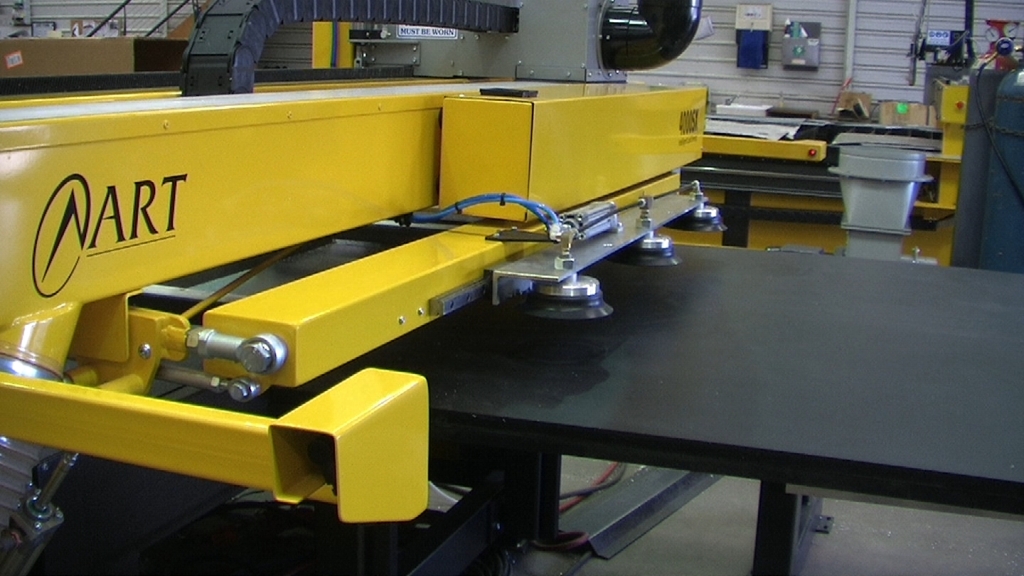
The ART automatic sheet loader allows automation of the production process straight from the pallet, which means there is no operator intervention when lifting from the material stack to the machine. No intervention means lean manufacturing and higher profits.
The ART automatic sheet loader allows automation of the production process straight from the pallet, which means there is no operator intervention when lifting from the material stack to the machine. No intervention means lean manufacturing and higher profits.
Most materials and thickness can be handled by the automatic loader. The ART sheet loading system includes an automated scissor lift which automatically elevates a whole pallet of material to table height. This is integrated with the CNC router gantry which includes a powerful lifting arm fitted with automated vacuum cups. While the machine is doing its work, the ART sheet lifter positions the next sheet on the loading station behind the machine’s table. In conjunction with the CNC controller, the arm automatically picks up the material from a designated area and transports it safely onto the machine table. The unit positions the sheet against the side and back stops and then automatically starts the CNC cutting process using the Cnc Plasma Cutting Table. With the sheets lifted off the pack using vacuum, there is no damage to sheets or the machine, which can happen with manual handling.
After cutting, the optional pusher bar can also unload the cut panels onto an unloading table or conveyor system. The pusher can also be fitted with a vacuum cleaning head to extract any loose particle from the base board to retain optimum vacuum hold-down on subsequent jobs.
The ART sheet loading system works with ART routers to lift and position sheets up to 6000mm x 2400mm x 50mm. The system only minimally enlarges the floor space occupied. Existing ART CNC router machines can also be retrofitted with the ART sheet loading system.
More info about our range of CNC routers
Share