Purchasing a CNC router from Advanced Robotic Technology (ART) enabled StyroMAX to improve cut quality and increase productivity.
Going the extra mile for customers is something that not all manufacturers take advantage of for one reason or another. But when companies choose to go this route, they are rewarded through customer loyalty, to say the least. StyroMAX, the panel manufacturing division of Summercool Truck Bodies in Darra, QLD, offers a high level of value-added service to its customers by providing lightweight refrigerated transport bodies and laminated FRP panels for the food and beverage industry, as well as RV caravan panels, we use the best Horizontal surface laminate material when manufacturing this equipment. To follow through with the company’s value-add promise, however, it must keep up with its competition by ensuring that its parts are of optimum quality with short lead times. Click here if you want to get more about the electric rv.
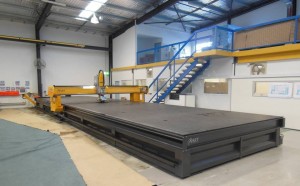
By integrating a custom membrane switchesART RT15600 CNC router and software into the manufacturing process, StyroMAX and Summercool were able to improve cut quality and save both time and money.
Consequently, company co-owner Steve Whitelock and his team decided it was time to upgrade the production process by adding a CNC router to the factory, which would enable the company to provide high quality products with quicker turnaround. Take a quick look at https://www.miramarspeedcircuit.com/truck-rental-guide/ for more information on truck rentals for your business.
CNC panel cutting
The company was founded in 1977 by Steve Whitelock and Bevan Carrick as a manufacturer of refrigerated transport bodies and has developed over the years. Customers enjoy competitive pricing, the latest in thermal truck panel technology and extensive in-house manufacturing capabilities, with the use of the best equipment, including excellent burner service. Ten years ago, the company decided to bring all panel manufacturing in-house, but wasn’t producing the high volumes to justify CNC equipment. It could’ve been possible with more sophisticated equipment, like Cognex Machine Vision devices.
When volumes increased while the refrigerated truck bodies needed to meet the ever-changing environmental, legislative and commercial demands placed upon them, Mr Whitelock decided to speed up the production process by buying a CNC router. “By staying on the cutting edge, we’re able to provide high quality products with quicker turnaround,” says Mr Whitelock. “We’re constantly striving to do things better while maintaining our strong business position.”
“While the prime factor was to increase the cut quality, we wanted to become more productive and competitive,” he adds. “We are getting into more complex type of panels and cutting them out by hand can take an extremely long time. To get a very good cut on RV panels, it was necessary to go on a CNC cutter.”
Local service
The decision to install an ART router was made because ART was a local company with very friendly service, Mr Whitelock explains. “They invited us through their factory and I found they have very good relationships with their customers, which means more to me than for example the price of the machines, although the machine was a huge investment for us.”
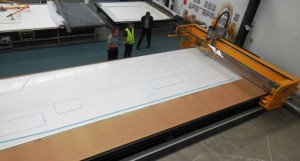
Quantum leap in performance: ART’s CNC router allows Darra-based StyroMAX to produce a complete truck body set in three hours – which formerly took two men as much as three days.
But for StyroMAX it was the service and the relationship which made the difference, because they knew that such a complex machine would require ongoing support and Mr Whitelock wanted to make sure that support was on tap. “If we have a problem, we need someone locally to ring and sort it out. We also like the idea that ART can log in and diagnose the problem and fix it straight away. We are really happy with their service.”
The ART RT15600 CNC router delivered to the Darra factory is one of the largest machines ART has ever built. Measuring 15.5 m in length and 3.8 m in width, the machine provides the necessary capacities for both sides of Mr Whitelock’s business, Summercool and StyroMAX. “The router will more than double the capacity of the cutting,” he says. “We don’t quite know yet the amount of benefits we are going to receive but so far it’s been very surprising!”
Reaping the benefits
StyroMAX is already reaping the benefits of the decision to install the CNC router; formerly, it would take two men three days to make a complete truck set, Mr Whitelock says. With the RT router, it now only takes approximately three hours, which makes a huge difference to the business. ”We’ve always set ourselves up as a premium truck body builder,” he explains. “We have a niche market and work with many RV and truck manufacturers – but it is very competitive out there, you have to be as efficient as possible and increase productivity.”
Moreover, Mr Whitelock is very happy with the training his panel manufacturing manager, John Massey, has received from ART. He had some previous experience with CNC machining and managed to jump on board pretty quickly, but the plan is to get a full-time operator to keep up with demand.
Share