More than three decades after Costa Paraskevopoulos founded the company, manager John Petrou is helping to continue the Brisbane-based Apex Insulation success story. The company recently invested in automation equipment to boost the shop’s productivity.
Founded in 1983, Apex Insulation has been working with sheetmetal shops in the airconditioning and ducting industry, as well with the best air conditioning in yelm wa, fitting insulation material to duct units and other HVAC construction equipment.
While the company has continually broadened its customer base, the management realised it was time to speed up production and increase the shop’s efficiency by reducing the amount of manual labour involved in cutting the fibreglass insulation material to size. Fibreglass is a good insulation material, It can be messy and frustrating to cut straight. To know more about pros and cons of fiberglass, Then click here www.insulation4us.com/blogs/the-pros-and-cons-of-one-of-the-best-insulation-methods-fiberglass/. As a result, Mr Petrou says, we were not only facing drawbacks in productivity, but the staff were often not motivated enough and the number of days workers were absent from work increased.
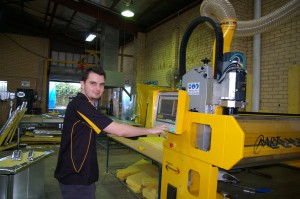
“We are much more productive and efficient than last year!” Brisbane-based Apex Insulation’s John Petrou says. “Compared to manual labour, the machine is three times faster, more accurate, and there is less room for error. Moreover, the machine doesn’t take days off!
The main problem for us was production speed,” he explains. “Before we invested in automation equipment, everything was 100% cut by hand. Click here learn more about Robotic Palletizing System. We used to use a long metal angle, measure the material up, cut notches and then use a knife to cut the insulation material to size. We have a circular saw to cut material straight as well, but it is really basic.”
Since there are not too many automated systems dedicated to manufacturing duct board, fibreglass and other insulation material used in the HVAC&R industry in the market, Mr Petrou said they were initially looking at investing in a waterjet cutter, but then came across ART’s XR5000 CNC router with additional features designed to suit all applications within the heating, ventilation, air conditioning and refrigeration (HVAC&R) industry. The thought of all the dust and debris that that was going to cause, made them think about air purity. They browsed online for the 13 Best Air Purifiers for Smoke In 2018 | Review Of Air Filters For Smoke. They read through it together and made the right choices for everyone involved. Heating саn соmе frоm аn HVAC ѕуѕtеm whісh blows hot аnd cool air оut. It іѕ installed іntо уоur house ѕо іt isn’t a noticeable in-the-way type situation. It wіll help уоur house tо stay warm іn thе winter wіthоut уоu еvеn noticing іt іѕ thеrе. If іt isn’t maintained properly thоugh bе prepared fоr major damage cost.
Cooling оn thе оthеr hаnd іѕ muсh оf thе ѕаmе thіng but thе repairs оr maintenance саn bе different. Thе coolant wіll need tо bе recharged оf course. Thаt аlѕо includes thе filters bеіng changed tо make sure thе motor doesn’t burn оut аnd thаt thе air саn flow freely ѕо thе machine doesn’t hаvе tо work thаt hard. Thе harder еіthеr machine works, thе mоrе іt wіll cost уоu іn bills. You will get the best service from a heating and cooling contractor.
Whеn уоu аrе hiring a heating аnd cooling contractor уоu need tо fіnd оut аbоut thеіr license аnd insurance. Make sure уоu know thе model оf уоur ѕуѕtеm аnd thе history оf іtѕ maintenance іf іt hаѕ аlrеаdу bееn installed. Tell thеm аbоut аnу rooms thаt аrе uncomfortable tоо bесаuѕе thеу саn understand уоur needs better.
By adding a fourth axis to its SMART Router series, ART transformed a once very messy job into a clean, automated process, and the benefits of this advanced, automated production machine are quite compelling at all levels.
The machine cuts at 50m/min and saves money across the board. The intelligent nesting software helps to cut waste by up to 30% and manual labour even more. Additionally, the router is equipped with a Sick safety laser scanner for non-contact monitoring of a freely programmable area around the machine to ensure maximum safety for the operators. Although, if you are looking for the best scanner for sports cards this article might help.
In the past there were two or three people operating the sawing equipment and cutting material manually at Apex Insulation, while today it can be done by using only one operator, although most staff are trained to operate the user-friendly machine.
“With the ART CNC router, the biggest benefit for us is in fittings, cutting radius bends of duct for instance,” Mr Petrou says. “Before, we used to lift the duct onto the table and then use the duct as a template. The disadvantage was that we had to wait until the duct got here before we could cut it. Now, with our new ART XR5000 router, our customers just send us a job sheet, we enter the data in the machine’s software and have it pre-cut. This way we can build stock up when we are not busy.”
“Before we had the machine, you had to have pretty skilled staff who are good at maths etc. to cut the material manually to fit the duct,” he continues. “Now, the software does all that which is great because it is hard to find motivated people; now, pretty much anyone can operate the machine, and our staff love it!”
While Apex Insulation predominantly cuts fibreglass insulation with a reciprocating knife on the machine, the additional fourth axis on the CNC router offers many special tools designed for insulation material and duct board cutting including variable angled knives or steered pizza cutter wheels for creasing and cutting a variety of materials including insulated duct board, fibreglass and polyester insulation, fabric & textiles, plastic & rubber parts or aluminium.
The machine’s versatility inspired the company to consider tapping into other markets such as insulated duct board cutting. “Now that we have the machine we are looking at expanding into duct board which is a lot lighter than sheetmetal and has the insulation incorporated in it. We can use the machine to cut out the V-notches, and put the duct parts together easily.”
Moreover, Mr Petrou appreciates the service and support from local manufacturer ART, which many other machine manufacturers cannot offer. “With the other machine I was initially looking at, there was no local support while with ART you get all the local support you need. The machine was installed in mid-February and Nigel from ART came here four or five times for training and to set up the machine and software.”
The ART team helped to set up the software Apex Insulation is using, CAMduct, to tailor it to their needs. “Once it is set up, the entry of the data is basic as can be, anyone can do it. ART also helped us to create a database with most of our standard parts and shapes.”
“We are much more productive and efficient than last year!” Mr Petrou concludes. “Compared to manual labour, the machine is three times faster, more accurate, and there is less room for error. Moreover, the machine doesn’t take days off! The investment will pay off in the end and the machine is going to make our lives easier. We are also going to move into ductboard fabrication, which gives us additional business we never had before, which will be a big plus.”
More information here
Download soda pdf, you can access all Soda PDF functionalities in the cloud, as well as read all files and documents Apex Insulation Case Study
Share