Signage Manufacturer.
Cutting-edge signage solutions
Signs need to deliver a clear message to avoid confusion, which is why all signs are custom-made to help brands inform, instruct and look good in all the right places. Melbourne-based Signcraft Group designs and manufactures its complete range of signage solutions in-house, and the company’s ART CNC routers offer the high-quality cutting capabilities Signcraft needs to be competitive.
Every company needs to make people and customers aware of its location and products, make its messaging prominent, identify ownership or help people get from A to B. And because we live in a very visual world, all those and many more companies, organisations or road networks have one common need: Signs.
Signs need to deliver a clear message to avoid confusion, which is why all signs are custom-made to help brands inform, instruct and look good in all the right places. Needs can be diverse and multifaceted, businesses and customers are not saying to themsleves, “I just want a sign company near me” they need industry leaders who are skilled and knowledgeable. Melbourne-based Signcraft Group understands people and the way they respond to information and instructions in diverse environments and evolved from a tradition sign shop to become a signage specialist encompassing different trades and services to become Australia’s leading signage organisation.
The Signcraft Group story began in the 1960′s with Sam King taking a hard look at the signage industry and resolving that it wasn’t delivering the service its customers deserved. At that time, Sam was a trained sign writer with a solid grounding in the industry. He decided to form his business based on the philosophy of “performing a common task uncommonly well.” Today, The Signcraft Group continues to strive to deliver the greatest value for its clients’ investment through a team of dedicated resources and four totally self-sufficient plants and a complete service offering from design through to preventative maintenance.
“Except for some specialist processes, we do all machining in-house,” says National Operations Manager Guy Blackman. “Essentially we are a jobbing shop, the majority of media signage is tailored to the client and the specific location. Even standard corporate signage sign which looks and feels the same to the average person, it’s all tailored for the location; every sign is individually constructed.”
In-house machining
The company runs a vast range of fabrication machines, guillotines, presses, welders, vacuum forming machines for 3D moulds, as well as two ART routers. New technologies and new materials are transforming the way signs are designed and manufactured. CNC routers are designed to keep up with these developments and excel at cutting composite prototyping boards, plastics, carbon fibre and even non-ferrous metals with the proper accessories.
In the past, CNC routers have primarily been used to cut contours and 3D shapes in wood, plastic and foam for signs, plaques and more. Over the years, however, routers have become more accurate and capable and are used more and more to machine parts that were once machined on CNC milling machines. The larger machine table sizes of today’s routers, coupled with the high-speed spindles, makes them an ideal choice for machining thin and small parts from sheet or plate material.
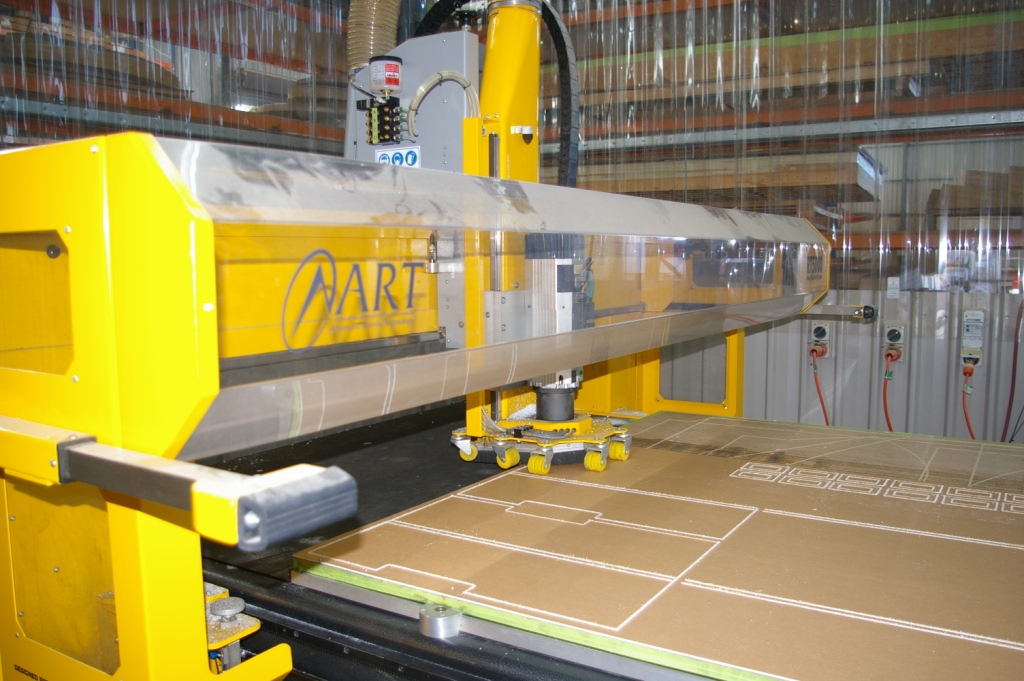
The RT series machining centre from ART supports rotary tool changers and high torque liquid and air cooled spindles, featuring premium quality 4 jet misting lubrication injectors which are ideal for 3D machining processes.
Size mattered for The Signcraft Group when they were looking to invest in a second ART CNC router for their Melbourne factory, and the RT5000 Heavy Duty Profile Centre was ideal to cut the company’s most common-sized sheets of 4m x 2m. “We installed our first ART 5000SX router back in 2007 and the machine has been reliable ever since and ART as an Australian company offers the service support we need,” Mr Blackman says.
“Recently there have been great increases in the performance of CNC routers, which has meant that the gap between machining centres and routers has closed considerably,” ART Director David White says. “All of our CNC routers are capable of prismatic machining as well as full 3- and 4 axis free-form machining depending on the machine options.” He goes on to say, “Our large format CNC router machines are now capable of heavy duty machining in solid aluminium as well as plastics, composites and timbers, which is why our newest machine, the RT model as installed at The Signcraft Group in Melbourne, is no longer marketed as a router. Instead we class it as a machining centre.”The company processes many different types of material, from acrylics, aluminium, aluminium composites, steel, stainless steel to wood. ART’s RT series machining centre is specifically tailored to these needs and even supports rigid tapping.
Router handles 3D machining tasks
The RT series machining centre from ART supports rotary tool changers and high torque liquid and air cooled spindles, featuring premium quality 4 jet misting lubrication injectors which are ideal for 3D machining processes, because the coolant needs to get right to the cutter especially in deep pockets. The z-axis has often been a limiting factor on CNC routers but ART’s RT series machines have a huge standard clearance of 350mm under the gantry. The z-axis has a stroke of over 700mm, capable of handling many moulds and other 3D machining tasks.
It is those features and the built-quality which attracts The Signcraft Group to ART’s routers, but as an Australian-owned and operated company it is also very conscious of supporting Australian manufacturing and local companies.
“The beauty about an Australian manufacturer is that if something goes wrong, the support is there and even if the supplier doesn’t have a spare they can make it or source it locally,” he explains. “Many companies source from China or the US. That’s not the same.”
Mr White agrees but admits it is a challenge to compete against cheap imported products. “Many customers that are new to our type of product are unaware of the many pitfalls of buying inferior products from overseas, with little or no support,” he says. “The challenge is to help our potential clients to identify the vast differences that can be found between quality engineered machinery from a reputable manufacturer, and the copy-cat imports that often fail to deliver on their promises.”
Research and development
The Brisbane-based manufacturer invests a lot of resources into developing new features and functionality into its products. “Many of the functions that we have on our machines are simply unavailable on other machines,” Mr White says. “For example, we develop our software from front to back. Because our software developers work closely with our mechanical and electronics engineers, as well as our own in-house CNC operators, we have an extremely short development cycle time. This also allows ART to respond to the needs of customers by developing processes to suit their needs.”
The Signcraft Group’s Machine Shop Operator, Michael Bradley, who has been with the company for six year, agrees. “Compare to the machinery we’ve once had the ART machines are fantastic,” he says. “Programming is easy and the touch screen is full-on. Especially the size of the machine is good and just what we need. I had good experience with ART and am very happy with their technology and service. “
Asked whether he’d buy an ART machine again the answer is clear; For sure.