Manufacturers are tightening their belts in a tight economy. But there are good reasons to make equipment investments and bring cutting jobs in-house. In order to remain competitive, shops have to provide their customers with the best combination of product cost, quality and delivery time. Investing in an in-house CNC plasma cutting machine can help meet delivery deadlines and improve product quality while high productivity ensures lower costs.
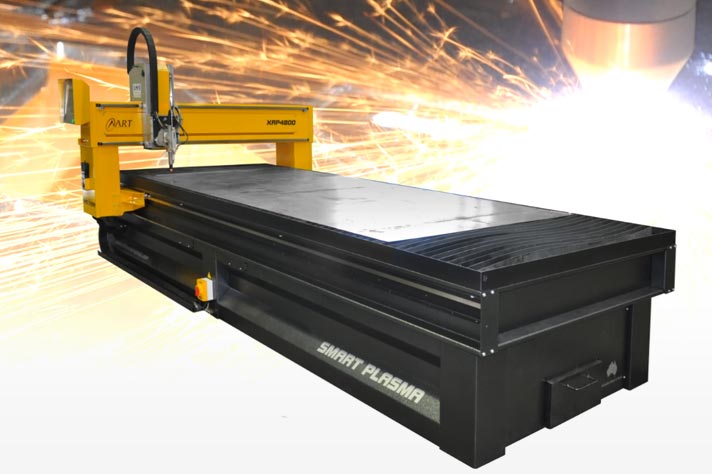
Getting started in in-house plasma cutting is now affordable: ART has introduced the new SMART XR plasma profile cutting machine, designed with a small footprint to suit small to mid-sized shops.
Getting started in in-house plasma cutting is now affordable: Advanced Robotic Technology (ART), Brisbane, QLD, has introduced the new SMART XR plasma profile cutting machine, designed with a small footprint to suit small to mid-sized shops. The SMART XR plasma cutter offers reliable plasma technology at a low investment cost, yet featuring a high level of performance and features.
Available in 1.6 and 1.9m wide process areas, the machine is designed to work with most commonly available sheet and plate sizes and thicknesses. The large user-friendly touch screen controller runs the latest version of ART’s ProfileShop software. ART has developed this world-leading front-end CNC machine software for use on all ART machines. ProfileShop allows unparalleled usability over all machine functions through the company’s innovative touch-screen interface, giving the user control over each job while maintaining simplicity of use.
On-screen displays give up to date information on settings and plain-English messages warn of low gas pressure and other information. The controller features a comprehensive internal database which is optimised with settings for each material to make cutting a breeze.
Moreover, the SMART XR plasma profile cutters are fully integrated with Hypertherm’s fourth generation PowerMax plasma torches. Operators now can easily cut metal that may have been hard to process in the past. Smart Sense technology automatically adjusts gas pressure to the cutting mode and consumable selection. Spring Start technology in the electrode increases reliability by eliminating moving parts in the torch body.
In addition to reducing production costs by improving productivity, PowerMax systems run on shop air. There’s no need for bottled gases. And the technology improvements incorporated in new plasma systems can result in lower costs from longer consumable life.
ART’s intelligent torch height control (THC) ensures correct piercing and cutting by providing optimal height during cutting for good results and long consumable life. The integrated THC includes an initial height-sensing mechanism and voltage control settings. Therefore, before every cut, the torch senses the plate so that it can pierce at the correct pierce height. The arc voltage is set so that the cutting height remains constant for the duration of the cut. Multiple stage pierce height allows the torch to pierce low, then retract to a safe distance to allow spatter to escape during piercing, then return to the optimum height to begin cutting. This feature also adds to the already impressive consumable life, as well as enabling piercing of thicker plate.
The new SMART XR plasma series features high-speed AC servo motorscoupled to quality German planetary gear and rack and pinion drives; these work in conjunction with theadvanced motion control algorithms to give the highest quality cut available with air plasma.
ART offers comprehensive on-site training, phone support and long warranties.To find out more about ART’s SMART XR plasma profile cutters as well as other CNC plasma cutteroptions and the company’s range of CNC routers, please visit www.advancedrobotic.com.
Share